US Port Labor Talks Turn on Automation Cutting Workers
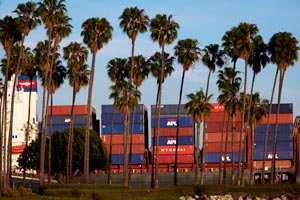
West Coast shippers and dockworkers are struggling to reach a labor agreement as terminal operators replace as many as half of laborers at some ports with robots in the largest technological change in half a century.
The two sides are discussing how to retrain and preserve jobs for dockworkers as automation reduces the number of positions at one Los Angeles terminal by 40% to 50% after changes are completed in 2016, according to a Harbor Department report released in April.
“In the U.S., the extent to which automation of container terminals affects the number of longshoremen’s jobs depends on negotiations between the employers and unions,” Neil Davidson, a senior analyst at Drewry Maritime Research in London, said by e-mail. “Employers aren’t simply free to decide to reduce jobs. In addition, it depends on the nature of the automation.”
The International Longshore and Warehouse Union and the Pacific Maritime Association are negotiating a new contract for 20,000 West Coast dockworkers, more than two months after a six-year agreement expired. A strike or lockout could cost the U.S. economy $2 billion a day, according to the National Retail Federation and National Association of Manufacturers.
In addition to automation, the two sides are discussing salaries and work rules. They resolved the issue of health-care expenses, they said in August without revealing details.
Terminal operators at the ports of Los Angeles and Long Beach, the largest U.S. port complex, are installing equipment that moves containers from ships to shore cranes and trucks with minimal human labor. The first large-scale automation project is scheduled to be complete at a TraPac Inc. terminal at the Port of Los Angeles in 2016. In neighboring Long Beach, Orient Overseas Container Line Asia Pacific Ltd. is adding robots as part of a $1.3 billion project to upgrade two container terminals by 2019.
“New technology is a fact of life,” said Craig Merrilees, a spokesman for the union. “The best approach is for workers and management to agree on terms that are fair and beneficial for all involved. That approach was successful when containers were introduced on the waterfront over 50 years ago, and it remains the best approach today.”
Wade Gates, a spokesman for the Pacific Maritime Association, representing shippers, declined to comment on the talks or the role of automation.
TraPac’s project will be the first fully automated port terminal on the West Coast, according to a September 2013 report to Los Angeles port commissioners. APM Terminals North America Inc. opened the first automated terminal in the U.S. in 2007, consisting of 30 remote-operated cranes at the Port of Virginia.
The 27 West Coast ports have come under increasing pressure from competitors in Texas and on the East Coast. In 2013, West Coast ports handled 43.5% of container cargo in the U.S., down from 50% in 2002, the Pacific Maritime Association said in a report this year. The expansion of the Panama Canal in 2015 will make it easier for cargo to and from Asia to bypass the West Coast in favor of Gulf Coast or Atlantic ports.
Against that backdrop, some allies of the dockworker union said automation is needed to keep West Coast ports from losing cargo to others, even at the cost of some jobs.
“If the port doesn’t automate, it will not be competitive,” said Branimir Kvartuc, spokesman for Los Angeles City Councilman Joe Buscaino, who represents the port area and was backed by the presidents of two longshore union locals in his 2011 campaign. “If it’s not competitive, it’s going to lose jobs anyway because of cargo diversion.”
Union and management haven’t estimated potential job losses from automation. The technology at TraPac’s terminal at the Port of Los Angeles is likely to reduce the number of workers needed per crane by about 53%, and at transtainers -- the hoisting devices for loading and unloading cargo from rail cars or trucks -- by 85%, according to the Los Angeles Harbor Department report.
Because part of TraPac’s terminal will be staffed conventionally, total job losses will equate to 40 % to 50 % of the 400-person workforce, the report said.
TraPac’s executive vice president in Los Angeles, Frank Pisano, said 1,500 non-union, casual workers are loading and unloading cargo each day due to backlogs. The casual workers are covered by terms of the labor contract and many expect to get hired and join the union, Merrilees said.
Automation should help reduce the backlogs without eliminating many permanent jobs, Pisano said by telephone.
“Automation means you’ll need mechanics to take care of the machines,” he said. “The ships are getting bigger. We’ve got to get them in and out quicker.”
Stephen Ng, director of trades for Orient Overseas Container Line, said the Hong Kong-based company’s automated container terminal in Long Beach will bring more cargo to the port, leading to 14,000 new jobs in Southern California.
The project “is supported by longshore workers who along with other stakeholders have been embracing the forward-looking advancements that will ultimately improve the port’s competitiveness, bring in more cargo, benefit the environment, and attract more business to the local economy,” Ng said in an e-mailed statement from spokesman Mark Wong.