Special to Transport Topics
Talent Wanted: Truck Technicians
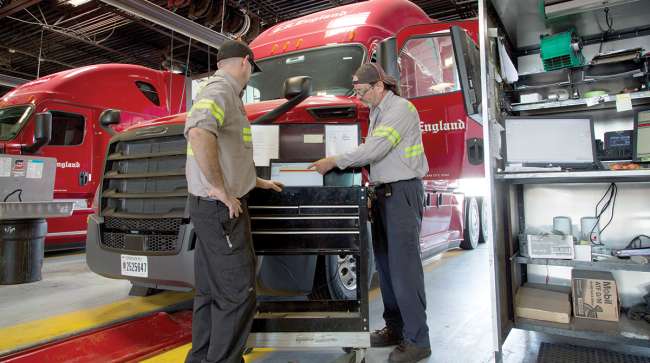
[Stay on top of transportation news: Get TTNews in your inbox.]
Trucking companies are pulling out all the stops to find, recruit, educate, train, develop and recognize the next generation of commercial vehicle technicians. It’s a fundamental issue as the industry’s workforce of technicians continues to age toward retirement, while at the same time, there’s a scarcity of young men and women coming into the profession to fill their ranks.
The challenge is as daunting — and as important to the industry’s success — as the ongoing battle to fill the chronic shortage of professional truck drivers.
Fleets are pursuing many strategies to entice more potential technicians to the field. They are casting a wide net, from shuttered factories to middle and high schools, community colleges, trade and technical schools, the armed forces and industry partnerships.
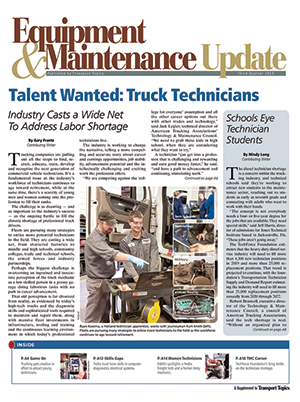
- Talent Wanted: Truck Technicians
- Schools Eye Technician Students
- FutureTech Champ Advances Her Career
- Former Army Mechanic Is Now a Truck Tech
- Electric Trucks Will Demand New Expertise
- The Technician's Vital Role in Trucking
- Understanding the Numbers Behind the Shortage
- Trucking Gets Creative in Attracting Young Technicians
- Clear Career Paths Needed for Technicians
- Closing the Skills Gap: Techs Must Master Diagnostics, Electrical
Perhaps the biggest challenge is overcoming an ingrained and inaccurate perception of the truck mechanic as a low-skilled person in a greasy garage doing laborious tasks with no path to career advancement.
That old perception is far divorced from reality, as evidenced by today’s high-tech trucks and the diagnostic skills and sophisticated tools required to maintain and repair them, along with massive fleet investments in infrastructure, tooling and training and the continuous learning environment in which today’s professional technicians live.
The industry is working to change the narrative, telling a more compelling and accurate story about career and earnings opportunities, job stability, advancement potential and the intellectually challenging and exciting work the profession offers.
“We are competing against the ‘college for everyone’ assumption and all the other career options out there with other trades and technology,” said Jack Legler, technical director of American Trucking Associations’ Technology & Maintenance Council. “We need to grab these kids in high school, when they are considering what they want to try.”
A technician “can get into a profession that is challenging and rewarding and earn good money faster,” he said, “and have a path to advancement and continuing, stimulating work.”
He said parents — and school counselors in particular — should do more to encourage children at the middle and high school levels to think about other paths besides the traditional four-year college degree, “where you come out with a [liberal arts or business] degree, $100,000 in debt, and then go sell insurance.”
Wiley Peters, vice president of maintenance at Denver-based Navajo Express, said today’s budding technicians want job security and the ability to advance. Peters started in the business 34 years ago washing trucks and trailers.
“They are very interested in a job that lets them continually expand and hone their skills,” he said.
Money doesn’t solve everything, Peters added.
“The personal interaction, the people you work with, a good work environment and good relationships, seeing that you’re respected and valued are as important if not more so than the money,” he said. “We preach it, teach it and live it. ... There is always room to grow and a path to advancement.”
Navajo recruits from vocational-technical schools and community colleges.
New hires are supported by a mentoring program that pairs them with an experienced technician, as well as online and computer-based training to continually develop and refresh their knowledge.
Navajo also engages with OEMs that come to Navajo shops and provide training and certification on their equipment.
“A technician nowadays does not spend 100% of their time with a wrench in their hands,” said Peters, noting that 50% or more is on the laptop, learning and doing diagnostics and troubleshooting. “Today’s technicians coming into the field are more comfortable with technology and online learning.”
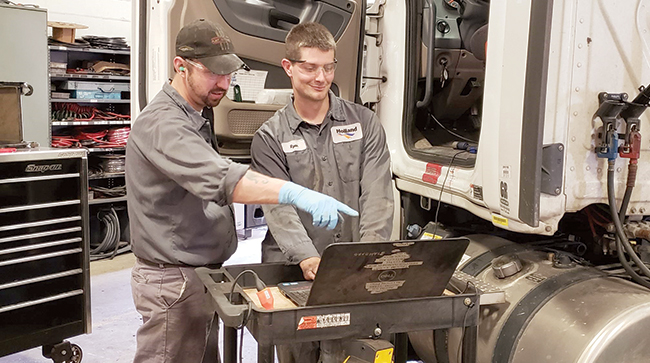
Ryan Kooima, a Holland technician apprentice, works with journeyman Kurt Smith (left). Fleets are pursuing many strategies to entice more technicians to the field as the workforce continues to age toward retirement.
Among the biggest challenges — and opportunities — is educating potential recruits on the diversity of technologies on today’s trucks and the excitement of working with ever-changing technology, said Doug Kading, vice president of maintenance for Salt Lake City-based C.R. England.
Today’s complex engines and drivetrains, their control modules and pollution control systems notwithstanding, “look at [all] the safety systems, forward-facing cameras, collision avoidance radar, anti-lock brakes, rollover mitigation, ELD, satellite and cellular systems.”
“That’s a lot of technology,” he said. “It’s not just working on a diesel engine.”
Perhaps more important, said Kading, is promoting the profession’s earnings potential.
“We are transparent with our wage package to help them understand pay [and benefits], what the different pay levels earn and the advancement potential,” he said.
C.R. England targets high schools and community and technical colleges where they participate on advisory boards, help steer curriculum and provide equipment for students to use for training.
The fleet has in-house training programs and resources utilizing dedicated trainers, videos, computer-based learning and hands-on training in which new techs work with experienced technicians.
One unique recruiting channel in which C.R. England participates is Utah’s Diesel Technician Pathways Program, sponsored by the Utah governor’s office. Under this program, employers do outreach to high schools to educate students on the field and opportunities while they are still forming ideas on careers to pursue. C.R. England sponsors tours of their shops and equipment in support of the program “so they can check us out and see if they like the profession,” Kading said.
“You have to start [recruiting] young,” he added. “If you wait too long, they’ve already made the decision to do something else.”
Holland, the Midwest regional less-than-truckload carrier of YRC Worldwide, recruits for new technicians from community colleges and vocational and technical schools, including those that don’t focus on diesel trucks, such as aviation and automotive, said Joe Sturtz, Holland’s vice president of equipment and maintenance.
“If we find a quality individual willing to learn, has an aptitude for technical and mechanical things, we will help them acquire and develop those skills,” he said.
The Holland, Mich.-based carrier develops its new talent through a formal apprenticeship program, which over about four years, takes an entry-level technician through a learning and development process that, when complete, graduates them to a full journeyman technician. They also work with OEMs on equipment-specific training and education for their technicians.
“We have the infrastructure, the equipment and commitment to training,” Sturtz said. The company’s technicians “get a wide range of exposure to the different types of equipment, from pre-2004 emissions tractors to the latest and newest tractors with advanced technology and telematics,” he said.
One way to change perceptions is through the language used to describe the profession.
UPS Inc., which “streets” some 100,000 vehicles per day, has made a conscious effort to shift away from “mechanic” as a job description and emphasize “technician,” said Patrick Thompsen, information services manager in UPS’ automotive engineering group. “We are looking for people who have grown up with technology in their life.”
UPS partners with local colleges and tech schools and provides UPS equipment for students.
We are competing against the 'college for everyone' assumption.
Jack Legler
Technology & Maintenance Council
“We want to harvest those who come out of those schools and already have experience working on UPS equipment. That helps speed up the learning curve for them as they come to work as a UPS technician,” Thompsen said.
The company also has extensive, ongoing in-house training for entry-level through experienced technicians to help them continually upgrade skills and keep abreast of the latest equipment and technologies.
UPS also targets veterans exiting military service, interacting with 22 military posts throughout the United States. It provides job information to veterans and showcases opportunities for veterans to get support from, and pursue careers with, UPS as technicians as well as in other fields. And it emphasizes commitment to career advancement through UPS’ reputation for promoting from within.
UPS employs roughly 4,175 technicians throughout the United States.
Tom Hendricks is UPS’ director of learning and development in the automotive engineering group and once worked in a dealership as a mechanic. Starting with UPS as a loader in college, he’s stayed with the company, moving through roles in management, engineering and supervision.
Recalling how the job of a technician has changed over the years, he said, “back in the day, you could read a manual and just R&R [remove and replace] a part.
“Now there is a decision tree you have to go through to find and fix the problem,” he said.
Hendricks echoes some of the same experiences of other fleets in recruiting the younger generation.
“When you talk to high school students, it’s about perception ... [and what they say] when they go home and talk with their parents. If you say mechanic, they have a vision of an old dirty garage with grease on the floor.”
“That’s not the reality,” he said. “Today’s shops are clean, well-lit and well-organized. Every technician is conscious about health and safety, they are highly trained and very savvy with technology,” he said, adding that as professionals, they implicitly understand and embrace the role technicians play in putting a safe fleet out on the road every day. “Now their primary tool is a laptop.”
UPS technicians also have one of the industry’s best pay and benefit packages, a UPS spokesperson said. Entry-level technicians start at $30 to $31 an hour depending on the area of the country, and top out at between $36 and $37 an hour. They also have company-paid health and welfare benefits and a retirement plan.
And they can be trained and work on a wide range of vehicles. These include hybrid electric, compressed natural gas (CNG), liquefied natural gas (LNG) and renewable natural gas (RNG)/biomethane in addition to the traditional heavy-duty Class 8 diesel-powered tractor, and soon, all-electric semis.
Truck leasing and transportation firm Ryder System Inc. has 6,300 mechanics and technicians across more than 800 shops in the United States.
Outreach to young candidates early and often and promoting continual skills development and professional recognition for experienced technicians are two key focus areas, said Renee Fisher, Ryder’s director of maintenance learning and recognition.
Similar to TMC’s SuperTech competition, Ryder sponsors its own internal competition, dubbed Ryder TopTech, showcasing the skills of its professional technicians in North America.
In its 18th year, the 2019 program began with some 2,800 Ryder technicians who applied and were qualified. Interestingly, one of the workstations was designed by nine former champions, where contestants had to diagnose and solve a problem developed by those past champions.
Held this year in Indianapolis, Ryder technician Ken Bilyea bested all competitors to win the 2019 Top Tech crown, which came with a $50,000 cash prize.
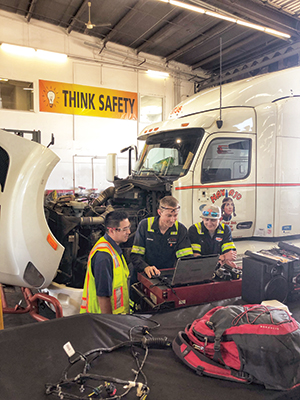
Navajo Express technicians check diagnostics. New technician hires at the fleet are supported by a mentoring program. (Navajo Express)
“The stations represent tasks or challenges techs are seeing every day or will expect to see,” Fisher said.
Ryder partners with equipment vendors to incorporate diagnostic challenges that involve the vendor’s products.
Fisher also sees recruiting efforts starting earlier, sometimes in middle schools.
“Some [students] don’t want to go on to secondary [college] education and are looking for other options,” and often get involved in trade-related clubs or activities in school, she said. “We target those, offer shop tours, help them learn more about the industry, what a technician does, possible career opportunities.”
The military also is a focus for recruiting, Fisher said. For those nearing the end of their active military service, Ryder has a program called Pathway Home, an accelerated 12-week training program near the local base where the soldier is stationed. Service members spend one day a week for 12 weeks learning various tasks and skills applied in Ryder’s shops. Pathway Home is offered at four locations, with one more to be launched this year and several others in the planning stages.
Similarly, equipment supplier and fleet operator Penske Truck Leasing has 750 locations in the United States and Canada that provide a footprint from which to recruit new techs. The company has some 140 partnerships with vo-tech schools nationwide.
“When we talk about partnerships, it’s not just showing up at career days,” said Ron Schwartz, Penske’s vice president of staffing. “Managers are on their advisory boards helping to develop curriculum. Shop managers go into schools and put on ‘Penske days’ to give them insight into the company and solving real-world problems.”
Those partnerships are supported by in-house training programs and resources, said Schwartz, who noted that in the past, training often was more of a one-size-fits-all approach.
“Not anymore. Training has to be tailored to the right level of expertise. It’s more iterative, a progression, completing prerequisites first,” he said. “We focus on the instruction being engaging, [building] programs based on methodologies of how people work and learn.”
The fact that trucks are now so complex from a technical standpoint means that today’s and tomorrow’s technicians must be tech savvy, said Schwartz, adding that new techs and 30-year vets alike are trained on specific skills-development modules to help them keep their knowledge up to date.
He cited Penske’s “How2” library of videos as an example.
“They’re short videos you can watch on a tablet. The technician can call up a video and see how a diagnostic or repair is done,” he said. That’s especially effective “with the younger generation who grew up on smartphones and tablets.”
Ultimately, fleets must access and employ every platform, tool and resource, however unconventional, to encourage and attract the next generation of technicians. That includes partnering with other industry groups, such as the TechForce Foundation, and developing new training tools and techniques, such as gamification, that more closely mirror how today’s students communicate, learn, access and absorb information, manage their day and interact with others, said Robert Braswell, TMC’s executive director.
Organizations such as the TechForce Foundation and its FutureTech Success program “tell a compelling story to students, guidance counselors, teachers and parents as to why to pursue a career as a technician, whether it’s auto, trucks or other industries that have technicians,” said Braswell, who notes that, among other activities, TMC is working with industry groups to develop apprenticeship standards for technician training programs across the country.
Reaching out to the next generation with familiar platforms and techniques — new to trucking but familiar to the younger generation – will be crucial, he believes.
One of those is gamification. In that regard, TMC is launching a game version of its TMC SuperTech competition for middle and high school students. “The goal is to attract ‘tactile’ learners,” Braswell said. (See related story on P. A4.)
The player is recognized for his or her success in beating the game and reaching higher levels of accomplishment. “It’s a compelling new way to reach people, especially a younger audience, reaching them where they live, through their smartphone,” Braswell said.