Warehouse Operators Look to Automation to Boost Capabilities, Ease Shortage of Labor

Warehouse operators are looking for ways to automate their operations to meet increasing demands for e-commerce fulfillment services and to compensate for what appears to be a growing shortage of workers.
Vendors are responding by offering a range of technologies, including intelligent robots that work alongside humans to find and retrieve stored items, high-speed packing and sorting machines that shorten the time it takes to process inbound and outbound loads, and software programs that provide complete visibility and tracking of shipments and products held in storage.
“Some of the largest distribution and fulfillment center operators in the United States have plans to automate almost every physical move in their facilities within the next two to three years,” said Mike Futch, executive vice president of Tompkins International, a supply chain consulting and research firm based in Raleigh, N.C.
The use of robots, Futch contends, will extend the capacity, hours of operation and life of distribution and fulfillment centers.
“Robots are more affordable than ever, and increasing wages and lack of available workers make the economics more attractive and justifiable than in the past,” Futch said.
There are many examples of automated warehouses in use around the world, and many more are planned, according to several industry experts interviewed by Transport Topics.
“The race to automate is on,” said John Hayes, a vice president at Vecna Robotics in Cambridge, Mass. “With e-commerce exploding and customer expectations on the rise, distribution and fulfillment centers, as well as third-party logistics providers, need an innovative way to reduce costs and increase throughput.”
Spending on warehouse automation in the United States and Canada is estimated to be $3.5 billion annually, and that figure is growing at a rate of 5% to 7% a year, according to Andy Williams, vice president of sales for SSI Schaefer, a German automation firm that does about one quarter of its total business in North America.
“The case for adoption is increasing due to consumer demand for a different type of service and labor availability,” Williams said. “Also, automation has matured and now is able to do jobs better than manual laborers.”
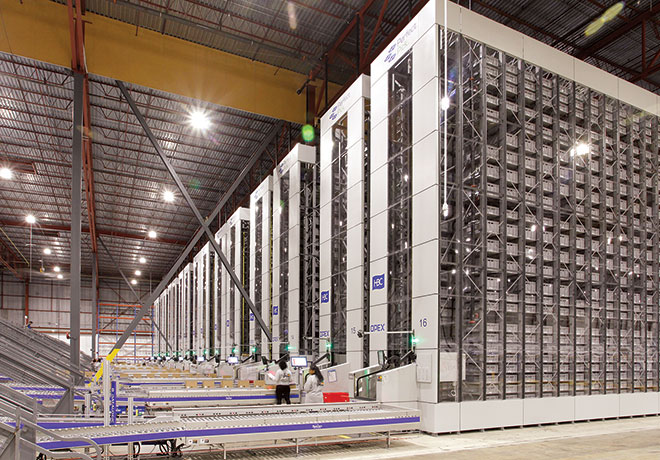
A new automated fulfillment center in Toronto can hold one million units of inventory for Hudson’s Bay Co. (Light Monkey Photography for Hudson’s Bay Co.)
In Toronto, the new Scarborough Distribution Center for Hudson’s Bay Co. features a robotic fulfillment system that is 12 to 15 times faster than traditional manual processes and can hold more than one million units of inventory for 89 Hudson's Bay stores in Canada. HBC also owns Lord & Taylor, Saks Fifth Avenue, Gilt and Home Outfitters in North America, Galeria Kaufhof in Germany and Galeria Inno and Sortarena in Belgium.

An RK Logistics employee loads up a robot, which takes a package to a shipping area, then returns to a staging area. (RK Logistics Group)
C&S Wholesale Grocers has deployed an automated robotic picking system in a new 500,000 square-foot distribution center in Newburgh, N.Y., and owner Rick Cohen has plans to roll out nearly a dozen fully automated food warehouses across the country. Automated warehouses can cut labor costs by 80% and are 25% to 40% smaller than typical warehouses, according to Cohen, who first invested in Symbotic LLC, a robotics company based in Wilmington, Mass., in 2007 and later bought the company.
C&S Wholesale Grocers ranks No. 77 on the Transport Topics Top 100 list of the largest private carriers in North America.
At RK Logistics Group in California, robots are used to move goods in a warehouse in Livermore, freeing up workers to do other tasks, according to Kip Shepard, a vice president at the company and a former manager at Consolidated Freightways.
“It improves the quality of life for warehouse workers,” Shepard said.
After a successful pilot program, Shepard said that RK Logistics is now working with its vendor, Fetch Robotics, to produce larger robots that can move heavier palletized freight.
DHL Supply Chain is currently testing robots from several companies, including Fetch and Locus Robotics in Andover, Mass., in customer warehouses in Europe and North America.
“We are evaluating permanent install options in 2018,” said Adrian Kumar, vice president of solutions design. DHL Supply Chain ranks No. 4 on the Transport Topics Top 50 list of the largest logistics companies in North America.
While automation can streamline the way warehouses operate, it also can change the way facilities are designed and built.

Storage racks at the McLane Ozark Distribution Center in Republic, Mo., are 105 feet tall and use automated machines to store and retrieve items. (McLane Co.)
Robbie Wainwright, vice president of logistics and engineering at McLane Co., one of the nation’s largest food service and grocery distributors, oversaw construction of the company’s first fully automated distribution center, which opened in 2012 in Republic, Mo.
The 370,000 square-foot McLane Ozark Distribution Center distributes groceries and merchandise to retailers in Missouri and Kansas and parts of Arkansas, Nebraska and Oklahoma.
“When we first started thinking about it, we had two choices,” Wainwright said. “Build a traditional center or a fully automated facility.”
For Wainwright, two things stood out about the use of automation and swayed the decision in favor of building the facility in Missouri. One was the ability to use height to accommodate more goods in a smaller space. The new distribution center is 10 stories high and uses robotic cranes to reach product on shelves that are the equivalent of 14 stacked pallets, or 105 feet, in height.
The other potential benefit that Wainwright saw was how robotic vehicles could be used to bring goods to people rather than the other way around, saving time and boosting productivity.
“Picking required a lot of walking around,” Wainwright said.
I see this as a competitive advantage. ... Facilities like this enable us to be very efficient.
Robbie Wainwright, vice president of logistics and engineering at McLane Co.
The new distribution center also incorporated other technologies, such as wrist-held scanners to identify products and machines that automatically take apart inbound pallets or put stretch wrap around outbound loads.
As a result, workers at the automated warehouse are 20% to 25% more productive than workers in McLane’s other distribution centers, Wainwright said. The facility also scores better in terms of safety and order accuracy.
“I see this as a competitive advantage,” said Wainwright, who has spent three decades at McLane and launched the company’s logistics department in 1993. “Facilities like this enable us to be very efficient.”
A second automated warehouse opened in Findlay, Ohio, earlier this year, and some facilities may be retrofitted to accommodate some automated features in the future, he said.
“We’re very interested in automated loading and unloading to assist drivers,” Wainwright noted.
McLane ranks No. 9 on the Transport Topics Top 100 list of the largest private carriers in North America.
There is broad support for automation among manufacturing and supply-chain executives, according to MHI, a trade association representing the material handling, logistics and supply chain industry.
In a survey, 80% of executives said the digital supply chain will be the predominant model within five years and 92% listed robotics and automation as one of nine technologies that could be a source of competitive advantage or disruption in the next decade.
The other technologies were inventory and network optimization, sensors and automatic identification, cloud computing and storage, predictive analytics, wearable and mobile communications, autonomous vehicles and drones, 3D printing and the “internet of things.”
A key issue for many warehouse operators going forward will be figuring out how to integrate manual and automated processes.

An automated storage unit is used to speed up material handling functions in warehouses. (Knud Dobberke for Dematic North America)
“It’s common to have both process types in a modern warehouse,” said Ken Ruehrdanz, manager of distribution systems for Dematic North America in Grand Rapids, Mich. “The challenge lies in manually moving materials in a way that avoids downtime for automated machines. This requires software that can calculate as accurately as possible when the load transfer should be made.”
Warehouse execution software is specifically designed to meet this need, Ruehrdanz said.
Another driving force for adoption of warehouse automation is the growth of online commerce, industry experts said.
Amazon.com, the nation’s largest internet retailer, acquired Kiva Systems, a manufacturer of automated guided vehicles, for $775 million in 2012 and now has about 45,000 AGVs in its rapidly expanding network of fulfillment centers in North America.
With its recent purchase of Whole Foods Market, Amazon may be considering building a network of automated warehouses for groceries, according to a news report by Bloomberg.
MWPVL International, a consulting firm that specializes in logistics and distribution, estimates that just 8% of distribution centers owned by the 75 largest North American grocers are partially or fully automated.

Williams
“Automation is now a core business of Amazon,” noted Andy Williams of Schaefer Systems International. “The original fulfillment model was not automated, but it was mechanized. Their huge warehouses still take tremendous numbers of people to operate.”
With e-commerce also contributing to a trend toward smaller, more frequent shipments, goods are being loaded on floors in trailers rather than being palletized, and, Williams said, that could lead to changes in equipment and accelerate development of automated loading and unloading systems.
At traditional warehouses and distribution centers, manual processes simply are not able to achieve the level of throughput needed to handle e-commerce business and, Williams said, “All of this is complicated by peak shipping demands during the holiday season.”
To meet the need for automation in e-commerce fulfillment, investors are pouring money into the development of new more advanced robots that can operate alongside human workers inside existing distribution facilities.
For example, IAM Robotics, a company started by former robotics experts at Carnegie Mellon University in Pittsburgh, launched its first fully autonomous mobile picking robot in January at a facility in New York owned by wholesale pharmaceutical distributor Rochester Drug Cooperative.
6 River Systems, based in Waltham, Mass., a company founded by former executives of Kiva Systems, received $15 million in venture capital earlier this year to develop an automated picking system specifically for warehouses that handle e-commerce orders.
San Francisco-based Kindred Systems recently introduced a robotic assistant, called Kindred Sort, that can be programmed to pick up, scan and assemble a variety of products into orders.
In a blog on the company’s web site, Kindred co-founder George Babu described the significance of automation. “We are helping alleviate the massive pressures facing the industry, including significant online sales growth, labor shortages and a decades-long lack of advancement in supply chain technology,” he said. “Our dream is to create an environment where humans can work alongside machines to increase productivity and work towards the greater good of all.”