The Lost Art of ‘Gear Jamming’
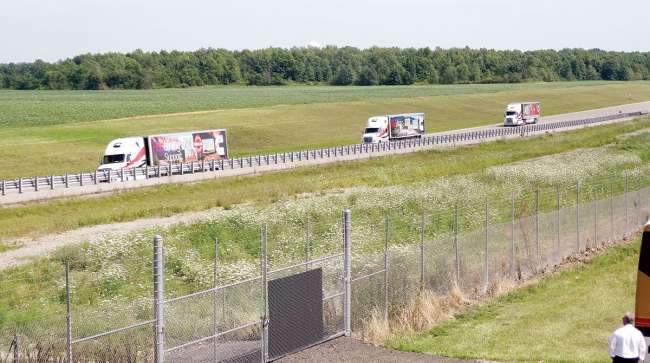
When Cummins Inc. invited industry journalists to the introduction of its X15, the new generation of its 15-liter truck engine, the event showcased not only the latest in heavy-duty truck engines, but also the evolution of transmission technology in trucking.
Members of the trade press were treated to test drives of several different vehicles at the Transportation Research Center, a proving ground near Marysville, Ohio.
Most of those trucks at the summer 2016 event were equipped with the X15 Efficiency version of the engine and automated transmissions with downsped drivetrains, but there also was a tractor equipped with the X15 Performance version with 565 horsepower and a 13-speed manual transmission.

Baxter
Offered a chance to drive, I accepted even though it had been a decade since I’d driven a vehicle with a constant-mesh transmission. This is one in which the gears are engaged and disengaged by locking and unlocking them from the main shaft.
I was able to quickly get the heavily loaded but powerful tractor up to speed using 11 gears, double-clutching throughout. That means releasing the clutch while the gear lever is in neutral to drag the transmission parts to the right rotating speed to smoothly engage the next gear. Timing is critical — but it’s easy once you get the hang of it.
This kind of shifting is a skill admired in traditional truck driving, and sung about by country singers. Their lyricists dubbed it “gear-jamming” because inexperienced drivers cause the transmission parts to clash with one another.
The 13-speed this truck had is particularly easy to shift in the upper gears because of something called compound shifts. The driver shifts the main gearbox the usual way, but the shift is accompanied by the action of the “splitter,” an auxiliary gearbox that shifts by air and effectively divides each gear in half. To compound shift, the driver flips the splitter button to the opposite position, then makes a lightning fast dash for the next gear with the standard gear lever. Smooth and fast.
Such manual shifting is becoming a lost art, however. Constant-mesh American boxes allow effortless, fast and smooth engagement of the next gear and even clutchless or “float” shifting.
Automated transmissions — only dreamed of in 1990 — are rapidly becoming standard. They allow a fleet’s vehicles to consistently cruise and accelerate in the most fuel-efficient gear, which keeps the rpm low. Also, the unit calculates the grade and load using the rig’s air spring pressures, as well as with a sensor called an “inclinometer.” That enables it to always start in the correct gear, avoiding abusive loaded uphill starts in third or fourth gear that save drivers time and effort, but destroy clutches and drivelines.
Automated boxes are rapidly becoming acceptable to old-school drivers because they precisely mimic the sophisticated shifting perfected by the “real” truck drivers of old.
Today, automated transmissions are offered by: Volvo Trucks North America with its I-Shift; Mack Trucks with its mDrive; Freightliner and Western Star with their Detroit DT12; Eaton Corp. with its Fuller Advantage series; the Eaton Cummins joint venture with its Endurant transmission; and Peterbilt and Kenworth with their Paccar transmission. Allison Transmission, meanwhile, offers the TC10 fully automatic, torque-converter type automatic.
Another advantage is that many automated transmissions perform better than traditional 10-speeds, the most common manual transmission. That’s because they have two additional gears, a feature that would make the box complex for manual shifting. The gears in a 12-speed are so close together that these automated boxes can skip every other gear during acceleration on level roads, which greatly speeds the process.
The icing on the cake is the universal use of “helical” gears, with subtly curved teeth in the 12-speed automated boxes. Helical gears last longer and virtually eliminate the gear whine drivers of old needed to tolerate hour after hour on the road.
The traditional, constant-mesh manual gearbox serves as the basis for these more modern designs. The 12-speed originated in Europe, where the precision of electronics allowed transmission makers to dispense with the synchronizers formerly used there for the first time. Synchronizers had removed the need for the driver to double-clutch and time the shift, but make for a heavier gearbox that needs more maintenance.
I have come to admire the amazing programming and smooth functioning of these new marvels of the road. I also recognize that opening up the driver pool and saving millions on fuel and maintenance are extremely significant accomplishments for this industry.
However, I have to admit I still miss the wonderful rhythms of “gear-jamming.” The roar of the diesel, and operating that clutch and gear lever in the right rhythm, make old-school truck driving a real adventure. It’s like the replacement of the steam locomotive with the diesel.
Despite the increase in efficiency and the tremendous reduction in terms of labor and maintenance, some of the romance, unfortunately, is now going away.